Expert Reverse Engineering Elicits Technical Data Necessary for Certification of Single-Use Bioreactor Systems
STEEL BIOREACTORS HAVE LONG BEEN THE SYSTEM OF CHOICE for manufacturing biological pharmaceuticals. That is because the traditional stainless steel design delivers the desired biological performance and meets regulatory guidance governing safe and effective use. Conventional bioreactors have some drawbacks, however, such as high capital costs and stringent cleaning and validation requirements. Single-use bioreactors, on the other hand, offer more economical bioprocessing solutions without compromising the quality of the drug.
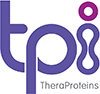
Therapeutic Proteins International, LLC (TPI) manufactures biosimilar active pharmaceutical ingredients for the worldwide market. The company develops generic versions of biological drugs whose patent protection has either expired or is expiring soon. Its patented MayaBio® single-use bioreactors enable bacterial proteins to be manufactured in two-dimensional plastic bags in a completely disposable system.
TPI created the first two prototypes of the MayaBio line with the goal of commercializing “the lowest-cost bioreactors and purification methods.” As with other bioprocesses, regulatory compliance is crucial for bioreactors. TPI was in need of the proper documentation to pass the certification before the single-use bioreactor systems would be commercially viable. Tek-Matic Inc., a Rockford, Ill.-based distributor of automation and motion control products, learned of TPI’s need and recommended AMD&E for the task.
AMD&E Approach
A COMPLETE SET OF ENGINEERING DOCUMENTS defines a product’s scope, function, and requirements. Occasionally, the necessary supporting documentation is unavailable and must be reconstructed. The Accelerated team began with the bioreactor prototypes and, through reverse engineering, gathered the technical data necessary for the essential documents. The project team worked backwards to construct accurate 3-D CAD models of the original products by analyzing the system designs and the interrelationships of components. Engineers verified the accuracy and validity of the designs.
Disposable bag and agitator: MayaBio single-use bioreactors enable bacterial proteins to be manufactured in two-dimensional plastic bags in a completely disposable system.
A Complex Process
BIOPHARMACEUTICALS REPLICATE PROTEINS that the body produces naturally. Biological drugs help treat people with cancer, anemia, rheumatoid arthritis, and other diseases. Biosimilars, while currently accounting for only about 2 percent of the overall biologics market, represent a strong and growing presence, driven primarily by rapidly rising health care costs and the expiration of patents on drugs.
Biologic products come into being through a complex set of processes. For many years, manufacturers of pharmaceuticals and vaccines have employed bioreactors to grow mammalian cells.
Because it involves living cells, the culture process is susceptible to contamination by bacteria, fungi, and viruses. Microbial impurities can diminish a drug’s potency. Searching for the source of contamination can result in lengthy shutdown periods and delays in manufacturing operations.
Strict controls ensure consistent product quality. Bioreactors precisely control temperature, dissolved oxygen levels, pH, and the speed at which a culture medium is agitated.
A typical system comprises a bioreactor, sensors, and actuators, along with a controller and software to monitor and control the conditions inside the vessel. Design rules for mechanical, electrical, and bioprocess engineering are described in the Current Good Manufacturing Practice (cGMP) regulations enforced by the U.S. Food and Drug Administration and Good Automated Manufacturing Practice (GAMP) guidelines.
Until about 15 years ago, biopharmaceutical manufacturers relied on massive stainless steel bioreactors that were expensive to install and operate. The conventional stainless steel vats must be sterilized and validated between batches in order to maintain a clean, sterile culturing environment. The advantages of single-use processing include no cleaning or sterilization (apart from traditional monitoring probes), minimal validation, reduced investment and running costs, and faster turnaround and setup times.
Flow meter: Strict controls ensure consistent product quality.
Disposable Bag-Mixing
THE MAYABIO IS A FULLY INTEGRATED SYSTEM equipped with multiple shelves, controller, displays, bags, and software. The low-profile unit resembles a pushcart measuring approximately 10ft L x 6ft H x 30in W. Wheels and casters facilitate easy movement between lab and production suites.
Paddles connected to the disposable bags constantly agitate the culture fluid through wave action. A heating element on the bottom side of each shelf keeps the fluid at a predetermined temperature for cell growth. Inflow of oxygen and removal of waste products occur automatically in this closed system.
Salient Features of the AMD&E Solution
EFFECTIVE REVERSE ENGINEERING depends on hardware and software working together. The hardware is used to measure an object, and the software recreates it as a 3-D model.
The Accelerated team did a careful analysis of the electronic and mechanical components before deciding on a final approach. Among several challenges faced during the course of the project were the increased complexity of the second-generation prototype compared to the first generation, the criticality of measuring different-shaped components to match the design intent, and the absence of original engineering drawings for an electrical enclosure.
Multilevel cart: The low-profile unit resembles a pushcart with wheels and casters for easy movement between lab and production suites.
The Accelerated team accumulated all of the technical data and instructions of how the products operate. This involved taking photographs, recording dimensions, retrieving part numbers, and reviewing available bill of materials. In some instances, disassembly was required. In others, it was necessary to obtain mounting information, sizes, shapes, and 3-D models of components from the manufacturers and suppliers.
“The excellent communication with the Accelerated team made this project possible and successful,” says Paul Marks, a quality control analyst at TPI. “They are very self-directed and diligent in their follow-through. Our interactions were a mixture of in-person meetings and numerous email and telephone exchanges. They were able to understand how everything was connected and convert the data they collected into professional AutoCAD drawings with true dimensional quality.”